High Volatge Leak Detection (HVLD) Technology
Based on annex 1 of good manufacturing practice (GMP) hundred percent container closure integrity testing (CCIT) of parenteral pharmaceuticals should be implemented before such medicines reached to the users. There are various deterministic and non-destructive methods suggested by Package Integrity Evaluation—Sterile Products USP 1207. Among those methods HVLD is one of the most reliable approaches that not only can reveal the existence of a leak by also the location of it. High voltage leak detection technology works by comparing the electrical current passing through inspection and detection electrodes at two different locations of the products. In case of a defective product, this current increases since current has a conductive path through the liquid inside the container. By comparing this over-current to that of good product’s current defective products can sort out from the inspection batch.
Inspection Principle
High voltage (V) is applied from inspection electrodes to a specific area of a sealed container made of non-conductive material. If the inspection area of the container is defective, current flows through pinhole, crack, or improperly sealed area in the solution (R) of the container. As a result of the loss of Z1 resistance in this figure, a change occurs in the amount of current. Detecting this change in the amount of current makes it possible to recognize the presence of a defect. The current is converted to a readable VDC in the electronic circuit to be displayed on the operation panel.
Current Calculation by Equivalent Circuit
Considering the above electrical circuit the good and defective current can be formulated and simplified as follows:]
Detection Accuracy
Our high voltage pinhole inspection machine has technology that can reliably detect even as small as 0.1 μm holes. These tiny holes cannot be found by human eyes or visual inspection. Our pinhole machines assure container closure integrity by targeting 0.1 μm holes which are even smaller than those φ0.2 μm of the filling filter mesh.
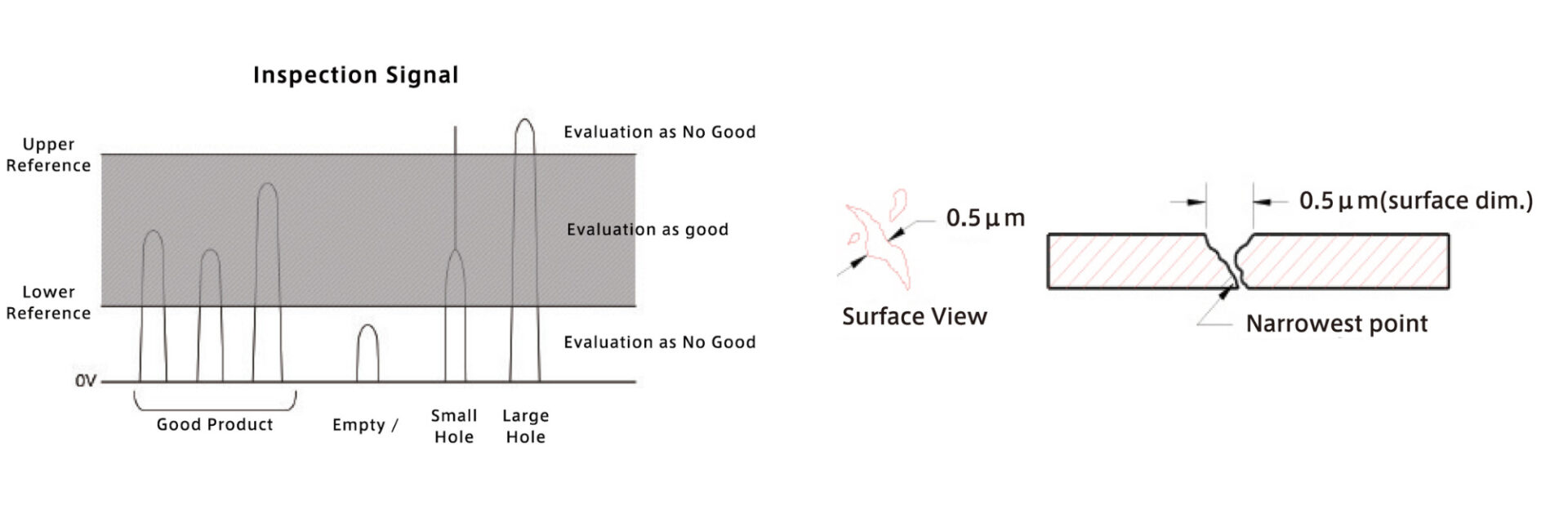
Software & UI
21CFR Part 11 & EU GMP Annex1 compliance and USP1207 recommended
Nikka Densok user friendly data management software and human machine interface (HMI) guarantees regulation compliance our software and HMI system makes it easy to manage the production data, inspection result data and signal trends with excellent display visibility.
Based on 21CFR part 11, various group management access levels can be defined based on user requirements to define various access levels. In addition, our system offers data transfer and backup using local folder and LDAP connection. Furthermore, event, alarm etc. data an be easily manage, analyze and can make hardcopy using the connected printer device.
Inspection Performance Validation
A specialized processing service company can create holes by laser drilling in microns. They are reliably detected by our machines. Nikka Densok cooperates with domestic and overseas laser processing service companies to support customer validation.
Furthermore, Nikka Densok is equipped with a KEYENCE laser hole drill instrument which can be used to make pinholes of around 50 μm.
Equipment Technology
Nikka Densok works with various PLC controllers manufacturing such as Mitsubishi Electric, Siemens and Allen Bradley. Customers have various options to choose from when it comes to electrical parts.
In addition, Nikka Densok develops various in-house electrical boards that use inside the machines. This enhances fast and cost effective access to these parts for customers.
Inline Inspection of IV Bags
Nikka Densok Advanced High Voltage Inspection Electrode Technology
Based on product shape and electrical conductivity this series comes with customized three to ten high voltage channels. As shown in the picture, each electrode has an inspection range based on the container size and electrical conductivity of the liquid. The four channels inspect the most vulnerable locations of the IV bag which are the body, port welding and sealing.
Nikka Densok has developed an advanced technology in designing customized inspection electrodes in that they have unique topology which makes it possible to concentrate the electrical current path toward any desirable area of the container. This ability makes it possible to inspect low electrical conductive liquids such as water for injection (WFI). In addition, based on the product specification and inspection speed our machine can offer leak detection of holes as small as 0.1μm.
Inline Machine Integration
Based on the production line layout as well as up-stream and down-stream machines, various infeed and discharge transportation methods such as manual or robot feeding as well as visual inspection integration is possible.
Such integration capability saves space and cost.
Furthermore, the discharge methods completely isolate the good and defective products to prevent any possibility of product mixture after inspection.
HDK Series Specifications
The following table shows the detail specifications of the HDK series.
Model | HDK |
---|---|
Inspection Station | 4+ Channels |
Processing Capacity | Up to 100 pcs/min (100 - 1000mL) |
Power Consumption | 5.0kVA |
Power Supply | 200 - 480VAC. 50/60Hz |
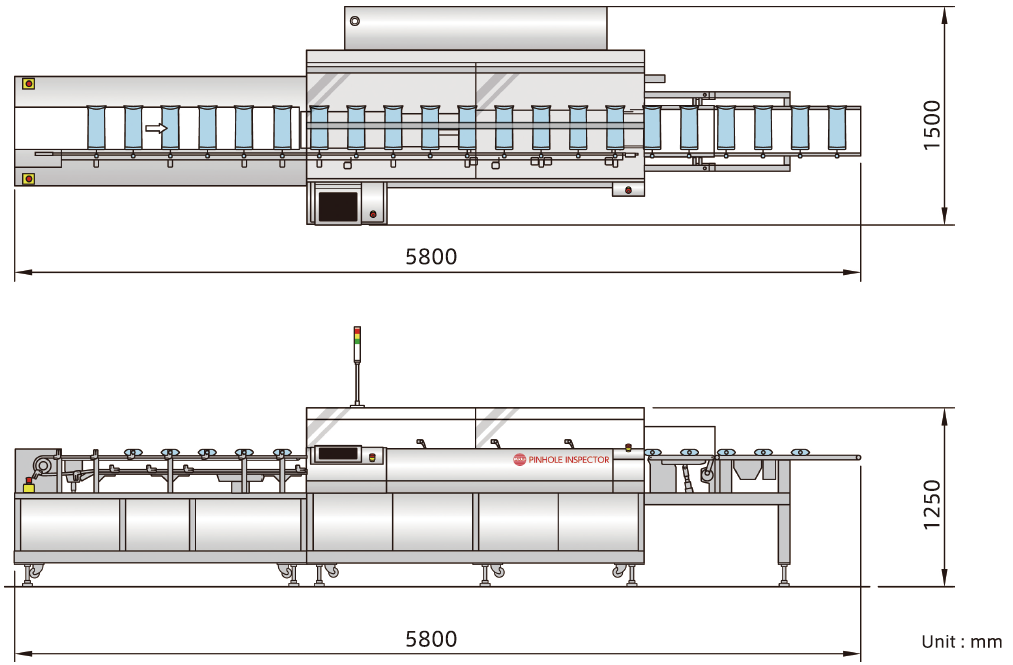